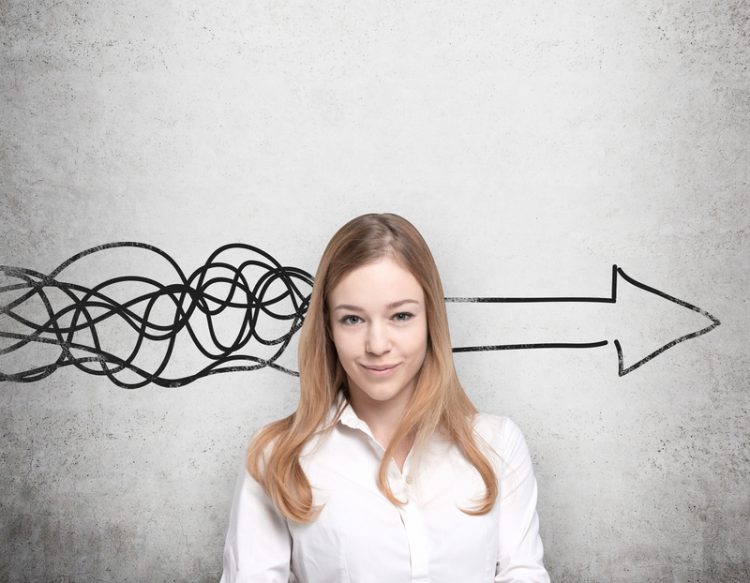
Have you ever been in a conversation where you did not understand what the other person was talking about but you didn’t want to say so? Back in the olden days (like 1996 or so), sitcoms on TV thrived on the confusion of the characters. Take the classic Seinfeld episode, “The Bottle Deposit.” George didn’t want to tell his boss that he had no idea what the boss wanted him to do on “the project” and spent the whole episode trying to obliquely gather clues. (Here he is, trying to decipher one.) George is Everyman and the writers knew that the need to not look stupid is strong in most of the population.
So it is that when others speak of what they do and we either don’t understand or have a different picture of the thing than the reality, we rarely ask for help deciphering the confusion. I’m sure I’m not alone in the Process Improvement world in the feeling that a lot of folks don’t have any idea what we do. In a previous article, I explained my process for process improvement but I think that there are also a lot of misconceptions about Process Improvement for those folks who kinda have an idea what it is.
Let’s see if we can address some here.
Misconception #1: Process Improvement is only for really big companies.
Some people think Process Improvement is only for either a really large business or perhaps a specific industry, like manufacturing. Actually, Process Improvement is for any business, large or small. Large companies may have higher ROI risks but all companies can benefit from documenting and optimizing their processes. In the E-Myth series, Michael E. Gerber does a fantastic job of laying out the reasons a very small shop needs to know, understand, and optimize processes. In The E-Myth Revisited, he says “The true product of a business is the business itself.” And the better the business runs its processes, the more valuable that product becomes. This is also true, as Gerber points out, for businesses as large as McDonalds.
Misconception #2: Large-scale, heavy systems are the only way to do process improvement
Another point of confusion is that in order to improve a process, a company would have to invoke some large-scale or heavy handed multi-consultant (i.e. expensive) “system” that begins to run their lives. Lots of acronyms and odd names start to come to mind there: Six Sigma, CMMI, TQM, JIT, Kaisen, Lean, Agile, DevOps, etc. These all have their own times and places to be implemented.
The “weight” of your process improvement effort should always be as small as you can get it while still seeing the benefits you need. Not all teams need a fully-structured Six Sigma program with 3-4 levels of belt holders working in them. I would argue this is, in practical terms, an exception case, albeit one that certainly does exist in the bigger companies. For some organizations, Lean might be the best fit – if eliminating waste is the driver of improvement. But if waste isn’t the biggest issue, a different approach might be better. A Process Improvement consultant should have multiple tools in his/her toolbox and know how to apply the lightest touch that gets the job done.
Misconception #3: Process Improvement just means that I now have more work and less freedom to get it done.
This last issue is more of a fear than a misconception. Folks believe that Process Improvement will lead to a workplace that is strict, tight, rote, and monotonous. Oh and, by the way, they also think it means they have to do more work. In reality, good Process Improvement is none of these things. Bad process improvement can be all of them.
The fear of many folks when Process Improvement is brought up in the workplace is that the humanity of the job is removed and replaced with one-size-fits-all answers. This should never be the outcome of a process improvement effort unless the goal is to optimize an automated production line where thousands of identical objects are created without variation.
But in the processes that involve people, there must be room for creativity and thoughtfulness while providing enough structure to still get the job done effectively. In nearly every Process Improvement project I’ve done there comes a point at which judgement calls must be made by the actors. Some processes have more than others. Engineering processes, for example, should outline the tasks and specify the data that must be passed on but should not presume to specify the engineering thought process, the problem solving creativity and experiential knowledge of the engineer. If all possible decision points and choices and all possible resultant paths are completely known, the entire process could be automated to take the human out of the equation completely. For some, this might be optimal; for most it is not.
What does Process Improvement really buy you?
Creativity and ability to think about the process is what leads to continuous improvement (CI). CI is a fancy of way of saying “don’t get stuck in a rut!” and “look for a way to do this better”. Done right, process improvement should lead to the mindset of continuous improvement. No process is 100% flawless and no company has 100% flawless processes. Not to mention that technology changes rapidly, constantly offering new tools and options than literally didn’t exist 6 months ago. At an absolute minimum, you should be continuously looking to take advantage of such advances.
The benefits of process improvement can be realized at any level of complexity. With optimized processes you get repeatability of the good parts of the process (good data, good hand-offs, faster completion) and less of the bad stuff (confusion, rework, delays due to lack of data or hand-off). Process Improvement also makes training new people much easier because you have a documented, thought-out, complete description of what needs to be done. If you want to have a software system that supports your processes (ERPs, databases, workflow management), Process Improvement is a critical first step to be sure you aren’t either (1) letting your technology dictate a bad process or (2) just doing dumb things faster with automation of bad processes.
In the end Process Improvement is all about better outcomes: better for the employees; better for the customers; better for the stakeholders. If the true product of the business is the business itself, improving the processes makes the business more valuable. Process Improvement makes the work flow more fluidly from inception to output, which makes for happier, more productive employees. To paraphrase Richard Branson, making your employees happier makes your customers happier.
Sandi Tepper is the VP of Technology Services at Provare Technology and is passionately committed to Making the world a better place, one team at a time. Follow us on Linked In.
Image Credit: © Denisismagilov | Dreamstime.com